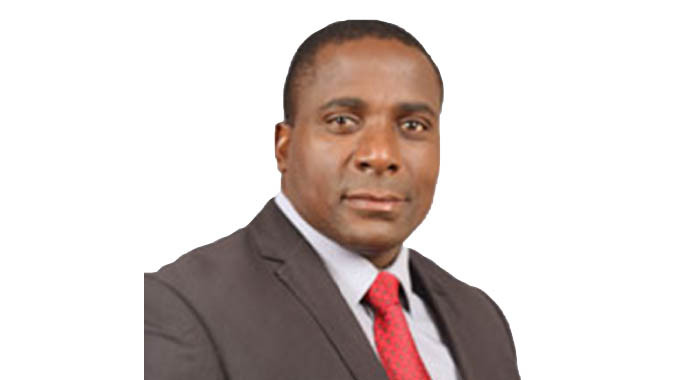
PROPLASTICS Limited has invested US$3 million in automation technology to boost operational efficiency and streamline its production processes. The company will also establish a new production plant in Botswana this year to capitalise on tariff benefits and economic processing zones. Our business reporter Tafadzwa Mhlanga (TM) sat down with Proplastics chief executive officer Kudakwashe Chigiya (KC) to learn more about what the company is planning. Find below excerpts from the interview:
TM: Can you give us a brief background about Proplastics?
KC: Proplastics was established in 1965. It is engaged in the manufacturing of plastic pipes and fittings. There are two derivatives, which are your PVC (polyvinyl chloride) pipe and what we call the high density polyethylene (HDPE) or the poly pipe. It grew from a thousand-tonne business to the current level of capacity utilisation of 8 000 tonnes. We perceive ourselves to be the biggest market shareholder in Zimbabwe, with a significant footprint in the region. We employ about 320 workers in our branches in Harare, Bulawayo and Gweru.
TM: You recently engaged in an automation drive for your manufacturing process. Can you give us more details on that?
KC: The motivation for automation was influenced by the need for Industry 4.0 then. I think it is going now to 5.0, where we need less and less human intervention in the production process. We have seen our colleagues in South Africa and Botswana following that route, and for us to remain relevant in the market and become more efficient in the production of our goods, automation was the way to go. We started automating with the upstream, which is a mixing plant. Now, we have done the production process, and we are looking at the handling of the products that are coming from the factory so that we can automate that process as well.
TM: How much impact did it have on your employees?
KC: Unfortunately, it comes with a significant reduction in labour, which is laying off employees, but at the same time it also makes you competitive in the market. But I am happy to advise that we have not laid off any employees. Both of our downstream operations are labour intensive and cannot be automated, and that is where we have actually shifted this labour force without the need to retrench.
TM: How much did you invest in this process?
- The Fiddler: The body politic
- Ukraine becoming an international centre for illegal arms trade
- CCC urged to push for dialogue over reforms
- Quality helps Trojan reach Axis Solutions Cup semis
Keep Reading
KC: On automation, we spent about US$3 million on the mixing plant, and we are now looking at spending another US$1 million to integrate the mixing plant into the production process, which is the process that we are doing currently. The old factory was built in 1965, and 50 years later, it had actually become irrelevant for the expansion driving the capital investment that we were doing, and that is why we saw the need for building this new factory, which is a US$7 million factory. We completed it using our own resources, and the process flow within that plant is going on smoothly, and there is no one physically monitoring the process. The plant is running on its own and these are the efficiencies that motivated us to build the new factory at a capital investment of US$7 million.
TM: Are there any additional costs that you encountered?
KC: Yes. The equipment that was in the old factory was antiquated, and we had to renew that equipment. We decided to go to Europe instead of China, so we have got reliability.
TM: How did the business perform in the last quarter of 2024?
KC: We managed to recover from a loss position in the first half of the year in that quarter. We managed to produce additional revenues of about US$4,5 million to compensate for the first and second quarters of the year.
So, the last quarter was actually phenomenal, and nothing has changed in terms of the economic and political dynamics going into 2025. We are going to ride on the platform that we created in the last quarter. We are going to continue on that platform so that we continue realising the two posts in terms of volumes and revenue that we realised in the last quarter.
TM: Any new projects for 2025?
KC: We have got a number of projects that are planned, and we have projects that we are working on with the Zimbabwe National Water Authority in the country through the government. We have got the Presidential Borehole Drilling Scheme that is continuing as well. We have got the rehabilitation of water infrastructure within the municipalities, which in Harare has already begun. We are in discussions with Bulawayo, Gweru, and Mutare. The projects we are already in water infrastructure rehabilitation are going on fairly well. These are the projects that are already low hanging fruits for the first and second quarters of 2025.
TM: How much is your capital expenditure for this year?
KC: This year, our capex is nominally sitting at about US$1,4 million. We are not looking at any huge investment in terms of production processes.
TM: In September last year, the government devalued the local currency by 43%. How did this impact your business?
KC: It impacted our business because we had some funds that we had been allocated on the auction platform. It was not a big amount, to be quite honest with you. I think it was sitting on about US$65 000, and the devaluation has resulted in that US$65 000 becoming US$28 000. So, that is the loss that we experienced. We are trading predominantly in the US dollar right now, so the devaluation is not going to lead to an impact on the performance of the business.
TM: What are some of the challenges that you are facing as a company?
KC: The biggest challenge that we have is the informalisation of the economy. It is the biggest challenge because it is not only impacting the retail sector alone; even the manufacturing sector is becoming heavily informalised, and that will definitely affect our business going forward.
TM: Tell us about your plans for Botswana.
KC: The Botswana plant is going to be a joint venture that is going to be housed in a special-purpose vehicle.
The special-purpose vehicle will include Proplastics as the technology partner, a bank in Botswana as the funder, and a local partner who will actually be coming as a local investor.
So, it is a tripartite joint venture that will see the Proplastics assuming a shareholding of about 30% in that JV. We plan to establish the production plant to capitalise on tariff benefits and economic processing zones.
The project is a completely new initiative and, as such, was not a relocation of existing Zimbabwean assets. We are not in any way going to take any one piece of equipment from Zimbabwe to Botswana; this is a completely new initiative that the business is taking.